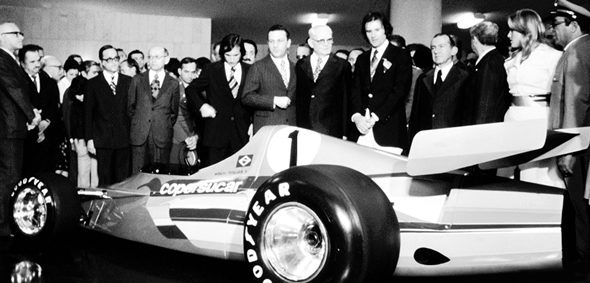
Depois de 356 dias de trabalho, desde a reunião na casa de Wilsinho, em 25 de outubro de 1973, o primeiro carro de Fórmula 1 brasileiro foi apresentado em grande estilo no Salão Negro do Congresso Nacional, com a presença do então presidente Ernesto Geisel. Wilson Fittipaldi Júnior partiu do nada e conseguiu vender seu sonho a um patrocinador por dois milhões de cruzeiros (atuais 3,063 milhões de reais) para começar a tornar realidade o primeiro carro brasileiro de Fórmula 1.
Na pré-história do computador, 18 pessoas trabalharam em regime de tempo integral para cumprir o cronograma de 10 meses. Gastaram 108 quilos de papel vegetal em 4.000 desenhos de suspensão traseira, 140 da dianteira, 280 do chassi monocoque e milhares de plantas de peças avulsas.
Aqueles que achavam que o carro brasileiro seria uma simples cópia disfarçada de algum protótipo daquele ano, ou uma mistura dos Fórmula 1 da época, surpreenderam-se ao deparar com um F-1 moderno, no mínimo diferente da mesmice existente. Se ia dar certo, era uma questão de testes, muitos testes, para concorrer com os europeus.
O Fitti FD-01 surpreendeu na apresentação. Era um carro sem dúvida bonito, muito mais aerodinâmico que qualquer outro da categoria e com grandes inovações no sistema de refrigeração. O radiador, não exposto, reduzia a área de atrito contra o vento, e as tomadas de ar, embutidas na carroceria, contribuíam para dar mais penetração aerodinâmica ao novo modelo.
Isso deixou entusiasmados os seis jornalistas estrangeiros convidados para o lançamento do Copersucar-Fittipaldi, representando as melhores revistas especializadas em automobilismo esportivo no mundo. Eles admitiram que era um veículo muito bem planejado, bem acabado e concebido nos mínimos detalhes, incluindo muitas novidades para a segurança do piloto.
No Fitti-1, apelido carinhoso pelo qual o carro vinha sendo tratado, o piloto ficava com a cabeça 15 centímetros abaixo da altura máxima da barra que o protegia das capotagens, enquanto nos similares essa margem de segurança era de dois centímetros. O revestimento interno, de material incombustível, diferia dos outros F-1, nos quais os pilotos ainda se sentavam sobre napa e plástico. Outra novidade estava na frente do Fitti F-1, onde se salientavam duas cavernas estruturais, moldadas em ligas especiais, com a função de canalizar mais ar para refrigeração do motor. Uma concepção moderna para a época.
A carroceria – cobrindo toda a traseira, inclusive o motor – e a entrada de ar embutida no santantônio (barra anticapotagem) deixaram o Copersucar-Fittipaldi com a menor área frontal – 1,07 m – em relação aos demais carros da Fórmula 1. Esse formato, além do benefício da farta refrigeração para o motor e os radiadores, diminuía muito o atrito da área frontal contra o vento. Essa solução recebeu o maior destaque dado pelos especialistas internacionais da época para o projeto de Ricardo Divila.
Wilson Fittipaldi exultava com a boa receptividade a seu carro, mas ainda não achava motivo para soltar rojões. Assim ele explicava as razões da cautela: “A aerodinâmica existente nos carros de F-1 neste início de década de 70 é limitada. A que projetamos em nosso carro, teoricamente, é mais funcional. E note que eu ressalto ‘teoricamente’ porque, na construção de monoposto, a distância entre a teoria e a prática é quilométrica. Em nossa opinião, os atuais carros da F-1 são um desastre, da parte do piloto para trás. O motor é exposto e os radiadores ficam pendurados para fora do carro, causando muita turbulência no confronto com o ar. Isso, em termos aerodinâmicos, é uma barbaridade. Simplesmente expor os radiadores fora do monocoque, à procura de maior refrigeração, é uma solução que se pode considerar ridícula, e lamentamos que ainda não se tenha tentado uma solução mais arrojada.”
Depois das críticas, a explicação: “Mas o fato de nunca terem feito não quer dizer que nós não devêssemos tentar, ainda mais quando a teoria indica que essa solução é muito melhor que as existentes. Então preferimos experimentar, em vez de simplesmente copiar os outros projetos. Foi uma iniciativa positiva, porque nos testes no túnel de vento que fizemos na Embraer, comparando nosso projeto com o Tyrrell F-1 convencional, conseguimos resultados muito melhores em penetração aerodinâmica e um índice de atrito menor.”
Uma boa surpresa constatada nos quatro testes de túnel de vento feitos na Embraer com o Fitti-1 foi em relação ao vácuo. Num cotejo direto com o Tyrrell 006, o caro brasileiro provocou menos formação de vácuo na traseira, o que tornava muito difícil ao carro que viesse atrás a ultrapassagem na reta.
Outra novidade do Fitti-1 era a posição de pilotagem. O piloto deveria dirigir praticamente deitado, uma novidade para deixar o protótipo mais raso e com centro de gravidade mais baixo. Wilsinho fazia questão de esclarecer que a posição do piloto dentro do carro poderia parecer ridícula, mas para ele era a ideal: “Tenho toda a comodidade para guiar e uma visibilidade excelente para todas as manobras. Quando Colin Chapman construiu o Lotus 25, em 1965, colocando Jim Clark para pilotar praticamente deitado dentro do cockpit, todo mundo se espantou, mas seis meses depois todos os demais carros copiavam a posição, pois, além de baixar o centro de gravidade do carro, oferecia mais segurança ao piloto”.
Todo esse trabalho significava, porém, apenas metade do caminho a percorrer. Seria preciso passar da teoria à prática. Wilsinho fez questão de salientar que, na teoria, o carro era perfeito, mas só a prática demonstraria sua competitividade. Os testes logo começariam, perfazendo um trabalho exaustivo para deixar o Fitti-1 pronto para o Grande Prêmio da Argentina, na abertura do Campeonato Mundial de Pilotos de 1975.
F-1 made in Brazil
Outro orgulho da Fittipaldi Empreendimentos – razão social da empresa – era o alto índice de nacionalização do carro. Tirando o motor, a caixa de câmbio e os freios usados na totalidade dos demais F-1, o restante do material empregado na construção do carro, 75%, era nacional: “O Fitti 1 é tão brasileiro quanto o Lotus é inglês”, afirmava Wilsinho. “Nem nós nem eles fazemos motores e pneus – e nós ainda fazemos algumas coisas a mais. Eles desenham as peças dos seus carros e mandam construí-lo fora, em fábricas especializadas. No Brasil não dispomos dessas firmas e tivemos de comprar máquinas para fabricarmos as nossas próprias peças, de acordo com a necessidade. Projetamos o monocoque completo, as pontas de eixo, as suspensões traseira e dianteira, o painel e as mangas de eixo, que são fundidas fora e usinadas na nossa sede. As molas e rodas foram feitas fora da fábrica, mas em São Paulo”.